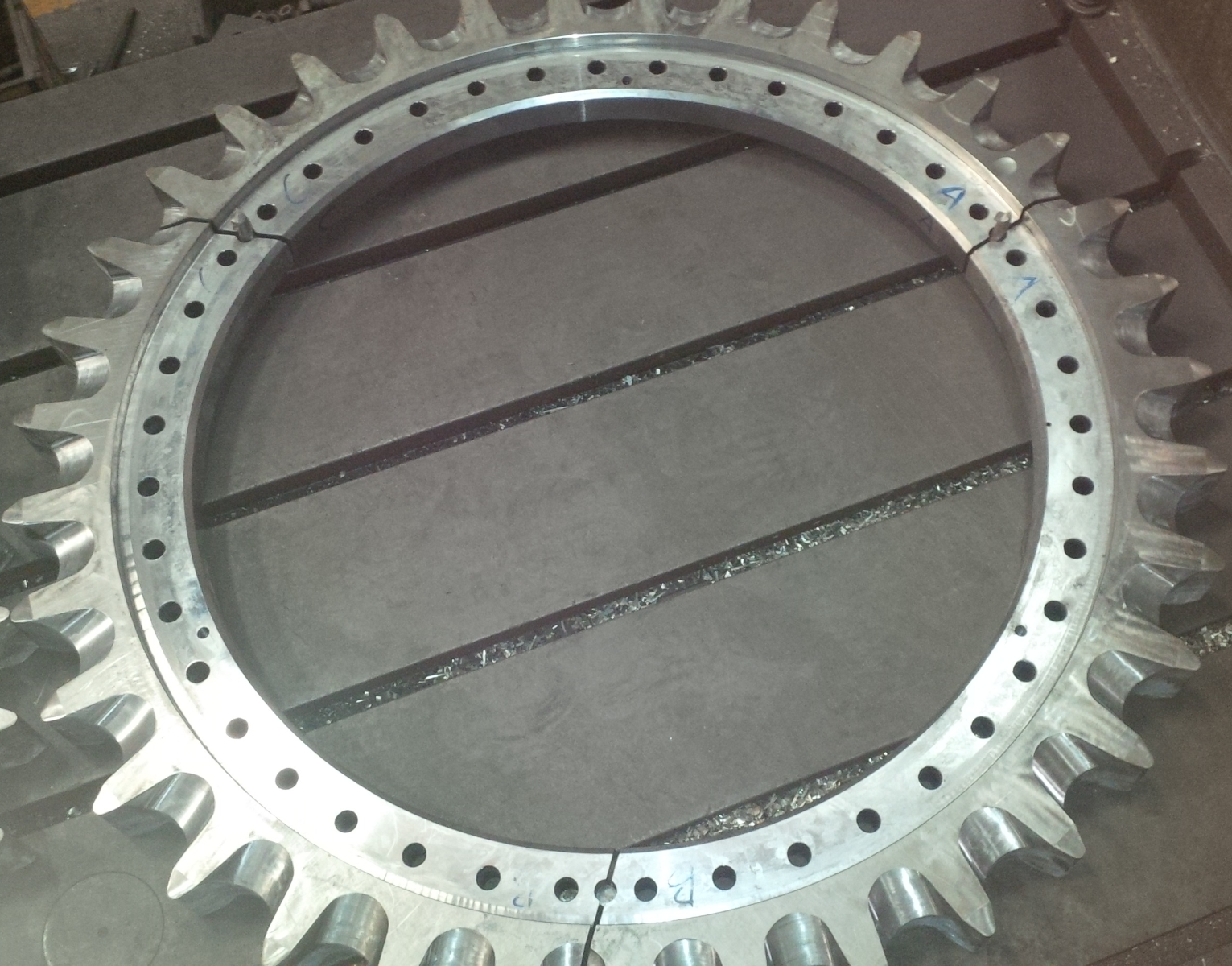
Guangzhou, Guangdong Jul 2, 2025 (Issuewire.com) - KLARM Machining, a leading specialist in precision manufacturing solutions in China, has officially expanded its technical capabilities and machining capacity to support the rapidly advancing field of power battery recycling. This strategic expansion responds directly to the growing demand for high-performance mechanical components in battery dismantling, sorting, extraction, and processing systemsvital infrastructure for the circular energy economy of the future.
As nations across the globe accelerate their transition to electric mobility and renewable energy, the volume of lithium-ion batteries entering end-of-life stages is rising at an unprecedented rate. From electric vehicles to grid storage systems, batteries are no longer peripheralthey are central to our modern infrastructure. Yet while the race to produce next-generation batteries has captured headlines, an equally important race is unfolding in the background: how to safely and efficiently reclaim valuable materials from used power batteries and reintroduce them into the supply chain. In this race, battery recycling equipment is taking center stage, and KLARM is ensuring that the machines behind the process are built on a foundation of uncompromising mechanical precision.
For years, KLARM has been known for its commitment to quality, speed, and engineering versatility. The company has built its reputation on serving high-tech sectors ranging from medical devices to aerospace, semiconductor to smart robotics. Now, by expanding its capabilities in CNC machining, Swiss turning, surface finishing, and tight-tolerance metrology, KLARM is positioning itself as a critical enabler in the power battery recycling ecosystem.
Eric Zhang, Technical Director at KLARM, emphasizes the strategic importance of the move: Battery recycling is not just about environmental stewardshipits about supply chain security, cost control, and long-term sustainability. The machinery required to dismantle, sort, and process used batteries is incredibly demanding from an engineering perspective. It must operate under high pressure, handle reactive materials, and maintain consistency over long cycles. Our role is to supply the critical CNC machined parts in China that make that performance possible.
KLARMs expanded offering includes high-precision parts for critical subsystems in battery recycling plants. These range from mechanical grippers and automated conveyors to component separators, electrolyte filtration systems, and high-pressure valves for thermal and chemical recovery units. Many of these systems require components machined to tolerances as tight as ±5 microns, with surface finishes that enable corrosion resistance, friction management, and chemical compatibility. For moving and sealing parts that must withstand acidic or alkali environments, materials such as stainless steel, titanium alloys, and specialized engineering polymers are essentialmaterials that KLARMs team is well-versed in machining with superior results.
Battery recycling equipment must also withstand extreme operational stresses. Crushing, shredding, and dissolving battery cells involve not only high mechanical forces but also the management of volatile compounds and potentially dangerous residues. Components like guide rails, alignment bushings, fluid couplings, and sealing collars must perform flawlessly despite abrasive exposure, pressure fluctuation, and thermal cycling. Failure of even a small part in a high-speed separator or filter housing can bring an entire plant to a haltor worse, pose safety risks.
KLARM addresses these challenges through a rigorous process that begins with DFM (design for manufacturability) collaboration and extends all the way through final inspection. Using advanced CAD/CAM software and a state-of-the-art workshop equipped with multi-axis CNC and Swiss-type lathes, KLARM can produce geometrically complex parts with internal channels, custom threads, and tight-fitting features. This capability is especially useful for custom tooling and adapter fittings used in pilot-scale recycling systems or newly commissioned lines.
To support this initiative, KLARM has also expanded its metrology lab with additional coordinate measuring machines (CMMs), non-contact optical inspection systems, and roundness testers. This ensures that every part leaving the facility matches not only the blueprint but the performance expectations required by high-throughput recycling facilities. Because downtime is expensive and spare part availability is often a bottleneck in global equipment rollouts, KLARM has invested in both rapid-turn prototyping and small-batch production capabilities. This allows the company to act as both a development partner and a scaled suppliersomething few in the precision machining industry can offer simultaneously.
More On Newsinterestcorp ::
- TrainerTrek Launches as India’s Premier Marketing Growth Platform for Coaches, Tutors, and Trainers
- Creative Floors and Designs Provides Flooring and Interior Design Services in Saddle Brook, New Jersey
- Kimberly Lynip, Recognized by BestAgents.us as a 2024 Top Agent
- Alisha Vars: A Beacon of Compassionate Care in St. Paul’s Nursing Community
- MiraSpaces Beta: The Creator-First Community Platform for Turning Passion into Profit
In addition to traditional battery chemistries like NMC (Nickel-Manganese-Cobalt) and LFP (Lithium Iron Phosphate), KLARM is preparing for the next wave of chemistries and formats entering the market. These include solid-state batteries, pouch-cell variants, and hybrid chemistries that may present new challenges in terms of disassembly, casing removal, or material segregation. KLARMs engineering team actively monitors industry research and collaborates with recycling equipment OEMs to anticipate future needs. By developing custom part libraries and modular tooling options, KLARM ensures that it can respond flexibly as the recycling landscape evolves.
One unique area where KLARMs expertise stands out is in the machining of micro-scale and high-aspect-ratio partsan advantage inherited from its Swiss machining heritage. Some battery dismantling systems require miniature grippers, clamps, and blade assemblies that operate with surgical precision. These parts may have features under 1 mm in diameter and must interact with battery cells of various sizes and conditions without causing shorts or ruptures. In such cases, machining errors are not just costlythey are unacceptable. Swiss-style lathes operated by KLARMs senior technicians ensure that even these ultra-small components meet exacting standards.
Environmental and regulatory factors are also shaping equipment designand, by extension, the components KLARM is asked to produce. Europe, North America, and parts of Asia are implementing Extended Producer Responsibility (EPR) rules that mandate traceability, material recovery targets, and equipment safety compliance. As a supplier, KLARM is adapting its workflow to integrate full traceability, batch documentation, and material certification. This includes laser engraving of serial numbers, RoHS and REACH-compliant surface treatments, and chemical compatibility testing for parts in contact with recovered electrolyte or cathode materials.
KLARM is also working closely with clients to improve the energy efficiency of recycling systems. Many battery recycling machines operate continuously and are energy-intensive, particularly during thermal treatment or solvent-based separation. By machining parts that enable lower-friction operation, tighter seals, and optimized flow dynamics, KLARM contributes indirectly to the energy performance of the recycling process itselfa growing concern as facilities aim to reduce their own carbon footprints.
Beyond production, KLARM sees its role as an engineering collaborator and R&D resource. For equipment startups working on novel battery disassembly methods or automated recovery processes, KLARM offers rapid-turn prototyping, material selection guidance, and part failure analysis. The company often becomes involved early in the design process to advise on manufacturability, tolerancing, and component simplificationhelping clients reduce cost and increase robustness before the first part is even cut.
KLARM leadership believes that the future of manufacturing will be defined by its relationship to sustainabilityand that precision machining services in China has an indispensable role to play. As we enter this next era of industrial development, machining isnt just about making things, said Zhang. Its about making the right things, with minimal waste, maximum reliability, and a vision for the lifecycle of each product. Battery recycling systems are one of the clearest expressions of this principle, and we are proud to contribute our capabilities to such a meaningful endeavor.
With this expansion, KLARM further solidifies its position at the intersection of advanced manufacturing and green technology. In an industry that is growing in both urgency and opportunity, the ability to deliver high-precision, high-performance parts at scale is not a luxuryit is a necessity. By investing in the machines, processes, and people required to meet that standard, KLARM is not only keeping pace with industry needsit is helping to define them.
Media Contact
Klarm Group Limited
Lanny Larm
Panyu, Guangzhou, Guangdong, China
Source :Klarm Group Limited
This article was originally published by IssueWire. Read the original article here.